Lignes d'injection de produits chimiques en fond de trou - Pourquoi échouent-elles ?Expériences, défis et application de nouvelles méthodes de test
Copyright 2012, Société des ingénieurs pétroliers
Abstrait
Statoil exploite plusieurs champs où l'injection continue en fond de trou d'inhibiteur de tartre est appliquée.L'objectif est de protéger la tubulure supérieure et la soupape de sécurité du (Ba/Sr) SO4orCaCO ;échelle, dans les cas où la compression de l'échelle peut être difficile et coûteuse à effectuer de manière régulière, par exemple le raccordement de champs sous-marins.
L'injection continue d'inhibiteur de tartre en fond de trou est une solution techniquement appropriée pour protéger le tubage supérieur et la soupape de sécurité dans les puits présentant un potentiel de tartre au-dessus du packer de production ;en particulier dans les puits qui n'ont pas besoin d'être pressés régulièrement en raison du potentiel d'entartrage dans la zone proche du puits de forage.
La conception, l'exploitation et la maintenance des lignes d'injection de produits chimiques exigent une attention particulière à la sélection des matériaux, à la qualification chimique et à la surveillance.La pression, la température, les régimes d'écoulement et la géométrie du système peuvent présenter des défis pour un fonctionnement sûr.Des défis ont été identifiés dans les conduites d'injection de plusieurs kilomètres de long depuis l'installation de production jusqu'au gabarit sous-marin et dans les vannes d'injection dans les puits.
Des expériences de terrain montrant la complexité des systèmes d'injection continue en fond de trou concernant les problèmes de précipitation et de corrosion sont discutées.Les études en laboratoire et l'application de nouvelles méthodes de qualification chimique sont représentées.Les besoins d'actions multidisciplinaires sont pris en compte.
Introduction
Statoil exploite plusieurs champs où l'injection continue de produits chimiques en fond de trou a été appliquée.Cela implique principalement l'injection d'inhibiteur de tartre (SI) dont l'objectif est de protéger le tubage supérieur et la soupape de sécurité de fond de trou (DHSV) contre (Ba/Sr) SO4orCaCO ;escalader.Dans certains cas, le briseur d'émulsion est injecté au fond du trou pour démarrer le processus de séparation aussi profondément que possible dans le puits à une température relativement élevée.
L'injection continue d'inhibiteur de tartre en fond de trou est une solution techniquement appropriée pour protéger la partie supérieure des puits présentant un potentiel de tartre au-dessus du packer de production.L'injection continue peut être recommandée, en particulier dans les puits qui n'ont pas besoin d'être pressés en raison du faible potentiel d'entartrage dans le puits de forage proche ;ou dans les cas où la compression de l'échelle peut être difficile et coûteuse à effectuer de manière régulière, par exemple le raccordement de champs sous-marins.
Statoil a une longue expérience de l'injection continue de produits chimiques dans les systèmes de surface et les gabarits sous-marins, mais le nouveau défi consiste à amener le point d'injection plus profondément dans le puits.La conception, l'exploitation et la maintenance des lignes d'injection de produits chimiques nécessitent une attention particulière sur plusieurs sujets ;tels que la sélection des matériaux, la qualification chimique et la surveillance.La pression, la température, les régimes d'écoulement et la géométrie du système peuvent présenter des défis pour un fonctionnement sûr.Des défis dans les lignes d'injection longues (plusieurs kilomètres) de l'installation de production au gabarit sous-marin et dans les vannes d'injection dans les puits ont été identifiés ;Fig. 1.Certains des systèmes d'injection ont fonctionné comme prévu, tandis que d'autres ont échoué pour diverses raisons.Plusieurs nouveaux développements de champs sont prévus pour l'injection chimique en fond de trou (DHCI);cependant;dans certains cas, l'équipement n'a pas encore été entièrement qualifié.
L'application de DHCI est une tâche complexe.Cela implique la complétion et la conception des puits, la chimie des puits, le système de surface et le système de dosage chimique du processus de surface.Le produit chimique sera pompé depuis le dessus via la conduite d'injection de produits chimiques vers l'équipement de complétion et vers le bas dans le puits.Par conséquent, dans la planification et l'exécution de ce type de projet, la coopération entre plusieurs disciplines est cruciale.Diverses considérations doivent être évaluées et une bonne communication pendant la conception est importante.Des ingénieurs de procédés, des ingénieurs sous-marins et des ingénieurs de complétion sont impliqués, traitant des sujets de la chimie des puits, de la sélection des matériaux, de l'assurance des flux et de la gestion des produits chimiques de production.Les défis peuvent être le roi des armes à feu chimiques ou la stabilité de la température, la corrosion et, dans certains cas, un effet de vide dû à la pression locale et aux effets de débit dans la ligne d'injection chimique.En plus de cela, des conditions telles qu'une pression élevée, une température élevée, un débit de gaz élevé, un potentiel d'entartrage élevé,un ombilical à longue distance et un point d'injection profond dans le puits, posent des défis et des exigences techniques différents au produit chimique injecté et à la vanne d'injection.
Un aperçu des systèmes DHCI installés dans les opérations de Statoil montre que l'expérience n'a pas toujours été couronnée de succès.Les défis varient d'un domaine à l'autre, et le problème n'est pas nécessairement que la vanne d'injection chimique elle-même ne fonctionne pas.
Au cours des dernières années, plusieurs défis concernant les lignes d'injection chimique en fond de trou ont été rencontrés.Dans cet article, quelques exemples sont donnés à partir de ces expériences.Le document discute des défis et des mesures prises pour résoudre les problèmes liés aux lignes DHCI.Deux histoires de cas sont données;un sur la corrosion et un sur le roi des armes à feu chimiques.Des expériences de terrain montrant la complexité des systèmes d'injection continue en fond de trou concernant les problèmes de précipitation et de corrosion sont discutées.
Des études en laboratoire et l'application de nouvelles méthodes de qualification chimique sont également envisagées ;comment pomper le produit chimique, potentiel d'entartrage et prévention, application d'équipement complexe et comment le produit chimique affectera le système de surface lorsque le produit chimique sera produit en retour.Les critères d'acceptation pour l'application chimique impliquent des problèmes environnementaux, l'efficacité, la capacité de stockage en surface, le débit de la pompe, si la pompe existante peut être utilisée, etc. et des matériaux aux abords de ces lignes.Le produit chimique peut devoir être inhibé par les hydrates pour empêcher le colmatage de la ligne d'injection par l'invasion de gaz et le produit chimique ne doit pas geler pendant le transport et le stockage.Dans les directives internes existantes, il existe une liste de contrôle des produits chimiques pouvant être appliqués à chaque point du système. Les propriétés physiques telles que la viscosité sont importantes.Le système d'injection peut impliquer une distance de 3 à 50 km de ligne d'écoulement sous-marine ombilicale et 1 à 3 km dans le puits.Par conséquent, la stabilité de la température est également importante.L'évaluation des effets en aval, par exemple dans les raffineries, peut également devoir être envisagée.
Systèmes d'injection de produits chimiques en fond de puits
Avantage de coût
L'injection continue d'inhibiteur de tartre au fond du trou pour protéger le DHS Vor le tube de production peut être rentable par rapport à la compression du puits avec un inhibiteur de tartre.Cette application réduit le potentiel d'endommagement de la formation par rapport aux traitements par compression de tartre, réduit le risque de problèmes de processus après une compression de tartre et donne la possibilité de contrôler le taux d'injection chimique à partir du système d'injection en surface.Le système d'injection peut également être utilisé pour injecter d'autres produits chimiques en continu dans le trou et peut ainsi réduire d'autres problèmes qui pourraient survenir plus loin en aval de l'usine de traitement.
Une étude approfondie a été réalisée pour développer une stratégie à l'échelle du fond de trou du champ S ou Oseberg.La principale préoccupation à l'échelle était CaCO;mise à l'échelle dans la tubulure supérieure et défaillance possible du DHSV.Les considérations de stratégie de gestion du tartre d'Oseberg S ont conclu que sur une période de trois ans, le DHCI était la solution la plus rentable dans les puits où les lignes d'injection de produits chimiques fonctionnaient.Le principal élément de coût en ce qui concerne la technique concurrente de compression du tartre était le pétrole différé plutôt que le coût chimique/opérationnel.Pour l'application d'inhibiteur de tartre dans le gas lift, le principal facteur sur le coût des produits chimiques était le taux élevé de gas lift conduisant à une concentration élevée en SI, car la concentration devait être équilibrée avec le taux de gas lift pour éviter le roi des armes chimiques.Pour les deux puits sur Oseberg S ou qui avaient des lignes DHC I fonctionnant bien, cette option a été choisie pour protéger les DHS V contre CaCO ;mise à l'échelle.
Système d'injection continue et soupapes
Les solutions de complétion existantes utilisant des systèmes d'injection chimique en continu sont confrontées à des défis pour empêcher le colmatage des lignes capillaires.Généralement, le système d'injection se compose d'une ligne capillaire, d'un diamètre extérieur (OD) de 1/4" ou 3/8", raccordée à un collecteur de surface, alimentée et connectée au support de tube sur le côté annulaire du tube.La ligne capillaire est fixée au diamètre extérieur du tube de production par des colliers de serrage spéciaux et s'étend à l'extérieur du tube jusqu'au mandrin d'injection chimique.Le mandrin est traditionnellement placé en amont du DHS V ou plus profondément dans le puits avec l'intention de donner au produit chimique injecté un temps de dispersion suffisant et de placer le produit chimique là où se trouvent les problèmes.
Au niveau de la vanne d'injection chimique, Fig.2, une petite cartouche d'environ 1,5" de diamètre contient les clapets anti-retour qui empêchent les fluides du puits de forage d'entrer dans la ligne capillaire.Il s'agit simplement d'un petit clapet monté sur un ressort.La force du ressort définit et prédit la pression requise pour ouvrir le clapet du siège d'étanchéité.Lorsque le produit chimique commence à s'écouler, le champignon est soulevé de son siège et ouvre le clapet anti-retour.
Il est nécessaire d'avoir deux clapets anti-retour installés.Une vanne est la barrière principale empêchant les fluides du puits de forage d'entrer dans la ligne capillaire.Cela a une pression d'ouverture relativement faible (2-15 bars). Si la pression hydrostatique à l'intérieur de la ligne capillaire est inférieure à la pression du puits de forage, les fluides du puits de forage essaieront d'entrer dans la ligne capillaire.L'autre clapet anti-retour a une pression d'ouverture atypique de 130-250 bars et est connu sous le nom de système de prévention à tube en U.Cette vanne empêche le produit chimique à l'intérieur de la ligne capillaire de s'écouler librement dans le puits de forage si la pression hydrostatique à l'intérieur de la ligne capillaire est supérieure à la pression du puits de forage au point d'injection chimique à l'intérieur du tube de production.
En plus des deux clapets anti-retour, il y a normalement un filtre en ligne, le but de celui-ci est de s'assurer qu'aucun débris de quelque nature que ce soit ne puisse compromettre les capacités d'étanchéité des systèmes de clapets anti-retour.
Les tailles des clapets anti-retour décrits sont plutôt petites, et la propreté du fluide injecté est essentielle pour leur fonctionnalité opérationnelle.On pense que les débris dans le système peuvent être chassés en augmentant le débit à l'intérieur de la ligne capillaire, de sorte que les clapets anti-retour s'ouvrent volontairement.
Lorsque le clapet anti-retour s'ouvre, la pression d'écoulement diminue rapidement et se propage dans la ligne capillaire jusqu'à ce que la pression augmente à nouveau.Le clapet anti-retour se fermera alors jusqu'à ce que le flux de produits chimiques accumule une pression suffisante pour ouvrir la vanne ;le résultat est des oscillations de pression dans le système de clapet anti-retour.Plus la pression d'ouverture du système de clapet anti-retour est élevée, moins la zone d'écoulement est établie lorsque le clapet anti-retour s'ouvre et le système essaie d'atteindre des conditions d'équilibre.
Les vannes d'injection chimique ont une pression d'ouverture relativement faible ;et si la pression de la tubulure au point d'entrée des produits chimiques devient inférieure à la somme de la pression hydrostatique des produits chimiques à l'intérieur de la ligne capillaire plus la pression d'ouverture du clapet anti-retour, un vide proche ou un vide se produira dans la partie supérieure de la ligne capillaire.Lorsque l'injection de produit chimique s'arrête ou que le débit de produit chimique est faible, des conditions proches du vide commenceront à se produire dans la section supérieure de la ligne capillaire.
Le niveau de vide dépend de la pression du puits de forage, de la gravité spécifique du mélange chimique injecté utilisé à l'intérieur de la ligne capillaire, de la pression d'ouverture du clapet anti-retour au point d'injection et du débit du produit chimique à l'intérieur de la ligne capillaire.Les conditions du puits varieront au cours de la durée de vie du champ et le potentiel de vide variera donc également dans le temps.Il est important d'être conscient de cette situation pour prendre les bonnes mesures et précautions avant que les défis attendus ne surviennent.
Avec de faibles taux d'injection, les solvants généralement utilisés dans ces types d'applications s'évaporent, provoquant des effets qui n'ont pas été entièrement explorés.Ces effets sont le gunking ou la précipitation de solides, par exemple des polymères, lorsque le solvant s'évapore.
En outre, des cellules galvaniques peuvent être formées dans la phase de transition entre la surface fluide du produit chimique et la phase gazeuse quasi vide remplie de vapeur ci-dessus.Cela peut entraîner une corrosion locale par piqûres à l'intérieur de la ligne capillaire en raison de l'agressivité accrue du produit chimique dans ces conditions.Des flocons ou des cristaux de sel formés sous forme de film à l'intérieur de la ligne capillaire lorsque son intérieur se dessèche pourraient bloquer ou boucher la ligne capillaire.
Philosophie de la barrière de puits
Lors de la conception de solutions de puits robustes, Statoil exige que la sécurité du puits soit en place à tout moment pendant le cycle de vie du puits.Ainsi, Statoil exige qu'il y ait deux barrières de puits indépendantes intactes.la figure 3 montre un schéma de barrière de puits atypique, où la couleur bleue représente l'enveloppe de barrière de puits primaire ;dans ce cas, le tube de production.La couleur rouge représente l'enveloppe barrière secondaire ;le boîtier.Sur le côté gauche du croquis, l'injection chimique est indiquée par une ligne noire avec un point d'injection vers le tube de production dans la zone marquée en rouge (barrière secondaire).En introduisant des systèmes d'injection de produits chimiques dans le puits, les barrières primaire et secondaire du puits de forage sont compromises.
Antécédents de cas sur la corrosion
Séquence des événements
L'injection chimique en fond de trou d'un inhibiteur de tartre a été appliquée dans un champ pétrolifère exploité par Statoil sur le plateau continental norvégien.Dans ce cas, l'inhibiteur de tartre appliqué avait été initialement qualifié pour une application en surface et sous-marine.La recomplétion du puits a été suivie par l'installation de DHCIpointat2446mMD, Fig.3.L'injection en fond de trou de l'inhibiteur de tartre en surface a commencé sans autre test du produit chimique.
Après un an de fonctionnement, des fuites dans le système d'injection de produits chimiques ont été constatées et des investigations ont commencé.La fuite a eu un effet néfaste sur les barrières du puits.Des événements similaires se sont produits pour plusieurs puits et certains d'entre eux ont dû être fermés pendant que l'enquête était en cours.
Les tubes de production ont été extraits et étudiés en détail.L'attaque de corrosion était limitée à un côté du tube, et certains joints de tube étaient tellement corrodés qu'il y avait en fait des trous à travers eux.Environ 8,5 mm d'épaisseur d'acier au chrome à 3 % s'étaient désintégrés en moins de 8 mois.La corrosion principale s'est produite dans la section supérieure du puits, de la tête de puits jusqu'à environ 380 m MD, et les joints de tubage les plus corrodés ont été trouvés à environ 350 m MD.Au-dessous de cette profondeur, peu ou pas de corrosion a été observée, mais beaucoup de débris ont été trouvés sur les diamètres extérieurs des tubes.
Le boîtier de 9-5/8'' a également été coupé et tiré et des effets similaires ont été observés ;avec de la corrosion dans la partie supérieure du puits d'un seul côté.La fuite induite a été provoquée par l'éclatement de la partie fragilisée du carter.
Le matériau de la ligne d'injection chimique était l'alliage 825.
Qualification chimique
Les propriétés chimiques et les tests de corrosion sont des points importants dans la qualification des inhibiteurs de tartre et l'inhibiteur de tartre proprement dit a été qualifié et utilisé dans des applications en surface et sous-marines depuis plusieurs années.La raison de l'application du produit chimique réel en fond de trou était l'amélioration des propriétés environnementales en remplaçant le produit chimique de fond de trou existant. Cependant, l'inhibiteur de tartre n'avait été utilisé qu'à des températures ambiantes de surface et de fond marin (4-20 ℃).Lorsqu'il est injecté dans le puits, la température du produit chimique peut atteindre 90 ℃, mais aucun autre test n'a été effectué à cette température.
Les premiers tests de corrosivité avaient été effectués par le fournisseur de produits chimiques et les résultats montraient 2 à 4 mm/an pour l'acier au carbone à haute température.Au cours de cette phase, il y avait eu une implication minimale de la compétence technique matérielle de l'opérateur.De nouveaux tests ont ensuite été effectués par l'opérateur montrant que l'inhibiteur de tartre était hautement corrosif pour les matériaux des tubes de production et du boîtier de production, avec des taux de corrosion dépassant 70 mm/an.Le matériau de la conduite d'injection chimique, l'alliage 825, n'a pas été testé contre l'inhibiteur de tartre avant l'injection.La température du puits peut atteindre 90℃ et des tests adéquats doivent avoir été effectués dans ces conditions.
L'enquête a également révélé que l'inhibiteur de tartre sous forme de solution concentrée avait rapporté un pH de <3,0.Cependant, le pH n'a pas été mesuré.Plus tard, le pH mesuré a montré une valeur très faible de pH 0-1.Ceci illustre le besoin de mesures et de considérations matérielles en plus des valeurs de pH données.
Interprétation des résultats
La ligne d'injection (Fig.3) est construite pour donner une pression hydrostatique de l'inhibiteur de tartre qui dépasse la pression dans le puits au point d'injection.L'inhibiteur est injecté à une pression plus élevée que celle qui existe dans le puits de forage.Il en résulte un effet de tube en U à la fermeture du puits.La vanne s'ouvrira toujours avec une pression plus élevée dans la ligne d'injection que dans le puits.Un vide ou une évaporation dans la ligne d'injection peut donc se produire.Le taux de corrosion et le risque de piqûres sont les plus élevés dans la zone de transition gaz/liquide en raison de l'évaporation du solvant.Des expériences de laboratoire réalisées sur des coupons ont confirmé cette théorie.Dans les puits où des fuites ont été constatées, tous les trous des lignes d'injection étaient situés dans la partie supérieure de la ligne d'injection chimique.
La figure 4 montre une photographie de la ligne DHC I avec une importante corrosion par piqûres.La corrosion observée sur le tube de production externe indiquait une exposition locale d'inhibiteur de tartre à partir du point de fuite par piqûres.La fuite a été causée par la corrosion par piqûres de produits chimiques hautement corrosifs et par une fuite à travers la conduite d'injection de produits chimiques dans le carter de production.L'inhibiteur de tartre a été pulvérisé à partir de la ligne capillaire piquée sur le boîtier et la tubulure et des fuites se sont produites.Les éventuelles conséquences secondaires de fuites sur la ligne d'injection n'avaient pas été prises en compte.Il a été conclu que la corrosion du tubage et du tubage était le résultat d'inhibiteurs de tartre concentrés appliqués de la ligne capillaire piquée sur le tubage et le tubage, Fig.5.
Dans ce cas, il y avait eu un manque d'implication des ingénieurs compétents en matériaux.La corrosivité du produit chimique sur la ligne DHCI n'a pas été testée et les effets secondaires dus aux fuites n'ont pas été évalués ;comme si les matériaux environnants pouvaient tolérer une exposition chimique.
Histoire de cas du roi des armes chimiques
Séquence des événements
La stratégie de prévention du tartre pour un champ HP HT consistait à injecter en continu un inhibiteur de tartre en amont de la soupape de sécurité de fond de trou.Un fort potentiel d'entartrage du carbonate de calcium a été identifié dans le puits.L'un des défis était la température élevée et les taux de production de gaz et de condensat élevés combinés à un faible taux de production d'eau.La préoccupation en injectant un inhibiteur de tartre était que le solvant serait éliminé par le taux de production de gaz élevé et que le produit chimique se produirait au point d'injection en amont de la soupape de sécurité dans le puits, Fig.1.
Lors de la qualification de l'inhibiteur de tartre, l'accent a été mis sur l'efficacité du produit dans les conditions HP HT, y compris le comportement dans le système de traitement en surface (basse température).La précipitation de l'inhibiteur de tartre lui-même dans le tube de production en raison du débit de gaz élevé était la principale préoccupation.Des tests en laboratoire ont montré que l'inhibiteur de tartre pouvait précipiter et adhérer à la paroi du tube.Le fonctionnement de la soupape de sécurité pourrait donc éviter les risques.
L'expérience a montré qu'après quelques semaines de fonctionnement, la ligne chimique fuyait.Il était possible de surveiller la pression du puits de forage à la jauge de surface installée dans la ligne capillaire.La ligne a été isolée pour obtenir l'intégrité du puits.
La ligne d'injection chimique a été retirée du puits, ouverte et inspectée pour diagnostiquer le problème et trouver les causes possibles de la panne.Comme on peut le voir sur la figure 6, une quantité importante de précipité a été trouvée et l'analyse chimique a montré qu'une partie de celui-ci était l'inhibiteur de tartre.Le précipité était situé au niveau du joint et du clapet et la vanne ne pouvait pas être actionnée.
La défaillance de la vanne a été causée par des débris à l'intérieur du système de vannes empêchant les clapets anti-retour de manger sur le siège métal sur métal.Les débris ont été examinés et les principales particules se sont avérées être des copeaux métalliques, probablement produits lors du processus d'installation de la ligne capillaire.De plus, des débris blancs ont été identifiés sur les deux clapets anti-retour, en particulier à l'arrière des clapets.C'est le côté basse pression, c'est-à-dire que le côté serait toujours en contact avec les fluides du puits de forage.Au départ, on pensait qu'il s'agissait de débris provenant du puits de forage de production puisque les vannes avaient été bloquées en position ouverte et exposées aux fluides du puits de forage.Mais l'examen des débris s'est avéré être des polymères avec une chimie similaire à celle du produit chimique utilisé comme inhibiteur de tartre.Cela a attiré notre attention et Statoil a voulu explorer les raisons de ces débris de polymères présents dans la ligne capillaire.
Qualification chimique
Dans un champ HP HT, il existe de nombreux défis en ce qui concerne la sélection de produits chimiques appropriés pour atténuer les divers problèmes de production.Lors de la qualification de l'inhibiteur de tartre pour l'injection continue en fond de trou, les tests suivants ont été effectués :
● Stabilité du produit
● Vieillissement thermique
● Tests de performances dynamiques
● Compatibilité avec l'eau de formation et l'inhibiteur d'hydrates (MEG)
● Test du roi des armes à feu statique et dynamique
● Information de redissolution de l'eau, produit chimique frais et MEG
Le produit chimique sera injecté à un taux de dosage prédéterminé,mais la production d'eau ne sera pas forcément constante,c'est-à-dire les coups d'eau.Entre les limaces d'eau,lorsque le produit chimique pénètre dans le puits de forage,il sera accueilli par un chaud,flux rapide de gaz d'hydrocarbure.Ceci est similaire à l'injection d'un inhibiteur de tartre dans une application de levage à gaz (Fleming et al.2003).
la haute température des gaz,le risque de décapage du solvant est extrêmement élevé et le gun king peut provoquer le blocage de la vanne d'injection.Il s'agit d'un risque même pour les produits chimiques formulés avec des solvants à point d'ébullition élevé/faible pression de vapeur et d'autres dépresseurs de pression de vapeur (VPD). En cas de blocage partiel.,débit d'eau de formation,Le MEG et/ou le produit chimique frais doivent être capables d'éliminer ou de redissoudre le produit chimique déshydraté ou encrassé.
Dans ce cas, un nouveau banc d'essai en laboratoire a été conçu pour reproduire les conditions d'écoulement à proximité des orifices d'injection d'un HP/HTg en tant que système de production.Les résultats des tests dynamiques Gun King démontrent que dans les conditions d'application proposées, une perte significative de solvant a été enregistrée.Cela pourrait conduire à un tir rapide et à un blocage éventuel des conduites d'écoulement.Les travaux ont donc démontré qu'il existait un risque relativement important d'injection chimique continue dans ces puits avant la production d'eau et ont conduit à la décision d'ajuster les procédures normales de démarrage de ce champ, en retardant l'injection chimique jusqu'à ce qu'une percée d'eau soit détectée.
La qualification de l'inhibiteur de tartre pour l'injection continue au fond du trou s'est concentrée sur le décapage du solvant et le pistolet de l'inhibiteur de tartre au point d'injection et dans la conduite d'écoulement, mais le potentiel de pistolet sur la vanne d'injection elle-même n'a pas été évalué.La soupape d'injection a probablement échoué en raison d'une perte importante de solvant et d'un canon rapide,Fig.6.Les résultats montrent qu'il est important d'avoir une vision holistique du système;ne pas se concentrer uniquement sur les défis de production,mais aussi des défis liés à l'injection du produit chimique,c'est-à-dire la soupape d'injection.
Expérience dans d'autres domaines
L'un des premiers rapports sur les problèmes liés aux conduites d'injection de produits chimiques à longue distance provenait des champs satellites de Gull fak sandVig dis (Osa et al.2001). dans la conduite via la vanne d'injection.De nouvelles lignes directrices pour le développement de produits chimiques de production sous-marine ont été élaborées.Les exigences comprenaient l'élimination des particules (filtration) et l'ajout d'un inhibiteur d'hydrate (par exemple du glycol) à tous les inhibiteurs de tartre à base d'eau à injecter dans les modèles sous-marins.Stabilité chimique,la viscosité et la compatibilité (liquide et matériaux) ont également été prises en compte.Ces exigences ont été approfondies dans le système Statoil et incluent l'injection chimique en fond de trou.
Au cours de la phase de développement du champ S ou Oseberg, il a été décidé que tous les puits devraient être complétés avec des systèmes DHC I (Fleming et al.2006). L'objectif était d'empêcher CaCO;mise à l'échelle dans la tubulure supérieure par injection de SI.L'un des défis majeurs en ce qui concerne les lignes d'injection chimique était d'assurer la communication entre la surface et la sortie du fond de puits.Le diamètre interne de la ligne d'injection chimique s'est rétréci de 7 mm à 0,7 mm (ID) autour de la soupape de sécurité annulaire en raison des limitations d'espace et de la capacité du liquide à être transporté à travers cette section a influencé le taux de réussite.Plusieurs puits de plate-forme avaient des conduites d'injection de produits chimiques qui étaient bouchées,mais la raison n'a pas été comprise.Trains de fluides divers (glycol,brut,condensat,xylène,inhibiteur de tartre,eau, etc.) ont été testés en laboratoire pour la viscosité et la compatibilité et pompés vers l'avant et en sens inverse pour ouvrir les conduites;cependant,l'inhibiteur de tartre cible n'a pas pu être pompé jusqu'à la vanne d'injection chimique.Plus loin,des complications ont été observées avec la précipitation de l'inhibiteur de tartre phosphonate avec de la saumure de complétion résiduelle de CaCl z dans un puits et le canon de l'inhibiteur de tartre à l'intérieur d'un puits avec un rapport élevé de gazole et une faible coupure d'eau (Fleming et al.2006)
Leçons apprises
Développement de méthodes d'essai
Les principaux enseignements tirés de l'échec des systèmes DHC I concernent l'efficacité technique de l'inhibiteur de tartre et non la fonctionnalité et l'injection chimique.L'injection en surface et l'injection sous-marine ont bien fonctionné au fil du temps;cependant,l'application a été étendue à l'injection chimique en fond de trou sans mise à jour correspondante des méthodes de qualification chimique.L'expérience de Statoil à partir des deux cas de terrain présentés est que la documentation ou les directives régissant la qualification chimique doivent être mises à jour pour inclure ce type d'application chimique.Les deux principaux défis ont été identifiés comme étant i) le vide dans la ligne d'injection chimique et ii) la précipitation potentielle du produit chimique.
L'évaporation du produit chimique peut se produire sur le tube de production (comme on le voit dans le cas du gun king) et dans le tube d'injection (une interface transitoire a été identifiée dans le cas du vide), il y a un risque que ces précipités soient déplacés avec le flux et dans la vanne d'injection et plus loin dans le puits.La vanne d'injection est souvent conçue avec un filtre en amont du point d'injection,c'est un défi,comme dans le cas de précipitations, ce filtre peut être bouché, provoquant la défaillance de la vanne.
Les observations et les conclusions préliminaires des enseignements tirés ont donné lieu à une vaste étude en laboratoire sur les phénomènes.L'objectif général était de développer de nouvelles méthodes de qualification pour éviter des problèmes similaires à l'avenir.Dans cette étude, divers tests ont été effectués et plusieurs méthodes de laboratoire ont été conçues (développées dans l'ordre) pour examiner les produits chimiques par rapport aux défis identifiés.
● Blocage des filtres et stabilité du produit dans les systèmes fermés.
● L'effet de la perte partielle de solvant sur la corrosivité des produits chimiques.
● L'effet d'une perte partielle de solvant dans un capillaire sur la formation de solides ou de bouchons visqueux.
Au cours des tests des méthodes de laboratoire, plusieurs problèmes potentiels ont été identifiés
● Blocages répétés du filtre et mauvaise stabilité.
● Formation de solides après évaporation partielle d'un capillaire
● Changements de PH dus à la perte de solvant.
La nature des tests effectués a également fourni des informations et des connaissances supplémentaires concernant les modifications des propriétés physiques des produits chimiques dans les capillaires lorsqu'ils sont soumis à certaines conditions.,et comment cela diffère des solutions en vrac soumises à des conditions similaires.Les travaux d'essai ont également identifié des différences considérables entre le fluide en vrac,les phases vapeur et les fluides résiduels qui peuvent entraîner soit un potentiel accru de précipitations et/ou une augmentation de la corrosivité.
La procédure d'essai pour la corrosivité des inhibiteurs de tartre a été élaborée et incluse dans la documentation en vigueur.Pour chaque application, des tests de corrosivité étendus ont dû être effectués avant que l'injection d'inhibiteur de tartre puisse être mise en œuvre.Des tests Gun King du produit chimique dans la ligne d'injection ont également été effectués.
Avant de commencer la qualification d'un produit chimique, il est important de créer une portée de travail qui décrit les défis et le but du produit chimique.Dans la phase initiale, il est important d'identifier les principaux défis pour pouvoir sélectionner les types de produits chimiques qui résoudront le problème.Un résumé des critères d'acceptation les plus importants se trouve dans le tableau 2.
Qualification des produits chimiques
La qualification des produits chimiques comprend à la fois des tests et des évaluations théoriques pour chaque application.Les spécifications techniques et les critères de test doivent être définis et établis,par exemple au sein du HSE,compatibilité matérielle,stabilité du produit et qualité du produit (particules).Plus loin,le point de congélation,viscosité et compatibilité avec d'autres produits chimiques,inhibiteur d'hydrate,l'eau de formation et le fluide produit doivent être déterminés.Une liste simplifiée des méthodes d'essai pouvant être utilisées pour la qualification des produits chimiques est donnée dans le tableau 2.
Concentration et surveillance continues de l'efficacité technique,les taux de dosage et les faits HSE sont importants.Les exigences d'un produit peuvent changer la durée de vie d'un champ ou d'une usine de traitement;varient avec les taux de production ainsi que la composition du fluide.Activité de suivi avec évaluation des performances,l'optimisation et/ou l'essai de nouveaux produits chimiques doivent être effectués fréquemment pour assurer le programme de traitement optimal.
Selon la qualité de l'huile,production d'eau et défis techniques à l'usine de production offshore,l'utilisation de produits chimiques de production peut être nécessaire pour atteindre la qualité d'exportation,exigences réglementaires,et d'exploiter l'installation offshore en toute sécurité.Tous les champs ont des défis différents, et les produits chimiques de production nécessaires varieront d'un champ à l'autre et au fil du temps.
Il est important de se concentrer sur l'efficacité technique des produits chimiques de production dans un programme de qualification,mais il est également très important de se concentrer sur les propriétés du produit chimique,comme la stabilité,qualité et compatibilité des produits.La compatibilité dans ce réglage signifie la compatibilité avec les fluides,matériaux et autres produits chimiques de production.Cela peut être un défi.Il n'est pas souhaitable d'utiliser un produit chimique pour résoudre un problème pour découvrir plus tard que le produit chimique contribue à ou crée de nouveaux défis.C'est peut-être les propriétés du produit chimique et non le défi technique qui est le plus grand défi.
Besoins spéciaux
Des exigences spéciales sur la filtration des produits fournis doivent être appliquées pour le système sous-marin et pour l'injection continue en fond de puits.Les crépines et les filtres dans le système d'injection de produits chimiques doivent être fournis en fonction des spécifications de l'équipement en aval du système d'injection de la partie supérieure,pompes et vannes d'injection,aux vannes d'injection de fond.Lorsque l'injection continue de produits chimiques en fond de trou est appliquée, la spécification du système d'injection de produits chimiques doit être basée sur la spécification présentant la criticité la plus élevée.C'est peut-être le filtre de la vanne d'injection au fond du puits.
Défis liés aux injections
Le système d'injection peut impliquer une distance de 3 à 50 km de conduite d'écoulement sous-marine ombilicale et 1 à 3 km dans le puits.Les propriétés physiques telles que la viscosité et la capacité de pomper les produits chimiques sont importantes.Si la viscosité à la température du fond marin est trop élevée, il peut être difficile de pomper le produit chimique à travers la ligne d'injection chimique dans l'ombilical sous-marin et vers le point d'injection sous-marin ou dans le puits.La viscosité doit être conforme aux spécifications du système à la température de stockage ou de fonctionnement prévue.Cela doit être évalué dans chaque cas,et dépendra du système.Comme le taux d'injection chimique de table est un facteur de succès dans l'injection chimique.Pour minimiser le risque de colmatage de la ligne d'injection chimique,les produits chimiques de ce système doivent être inhibés par les hydrates (si potentiel pour les hydrates).La compatibilité avec les fluides présents dans le système (liquide de conservation) et l'inhibiteur d'hydrate doit être effectuée.Essais de stabilité du produit chimique aux températures réelles (température ambiante la plus basse possible,température ambiante,température sous-marine,température d'injection) doivent être dépassées.
Un programme de lavage des lignes d'injection de produits chimiques à une fréquence donnée doit également être envisagé.Il peut avoir un effet préventif de rincer régulièrement la ligne d'injection chimique avec du solvant,du glycol ou un produit chimique de nettoyage pour éliminer les éventuels dépôts avant qu'ils ne s'accumulent et ne provoquent le colmatage de la conduite.La solution chimique de liquide de rinçage choisie doit êtrecompatible avec le produit chimique dans la ligne d'injection.
Dans certains cas, la ligne d'injection chimique est utilisée pour plusieurs applications chimiques en fonction de différents défis sur une durée de vie sur le terrain et des conditions de fluide.Dans la phase de production initiale avant la percée de l'eau, les principaux défis peuvent être différents de ceux de la fin de vie souvent liés à l'augmentation de la production d'eau.Passer d'un inhibiteur à base de solvant non aqueux tel que l'inhibiteur d'asphalte à un produit chimique à base d'eau tel qu'un inhibiteur de tartre peut poser des problèmes de compatibilité.Il est donc important de se concentrer sur la compatibilité, la qualification et les usages des entretoises lorsqu'il est prévu de changer de produit chimique dans la ligne d'injection chimique.
Matériaux
Concernant la compatibilité des matériaux,tous les produits chimiques doivent être compatibles avec les joints,élastomères,joints et matériaux de construction utilisés dans le système d'injection chimique et l'usine de production.Une procédure d'essai pour la corrosivité des produits chimiques (par exemple, un inhibiteur de tartre acide) pour l'injection continue au fond du trou devrait être développée.Pour chaque application, des tests de corrosivité étendus doivent être effectués avant que l'injection de produits chimiques puisse être mise en œuvre.
Discussion
Les avantages et les inconvénients de l'injection chimique continue en fond de trou doivent être évalués.L'injection continue d'inhibiteur de tartre pour protéger le DHS Vor du tube de production est une méthode élégante pour protéger le puits du tartre.Comme mentionné dans cet article, l'injection continue de produits chimiques en fond de trou présente plusieurs défis.,cependant pour réduire le risque il est important de comprendre les phénomènes liés à la solution.
Une façon de réduire le risque est de se concentrer sur le développement de méthodes de test.Par rapport à l'injection de produits chimiques en surface ou sous-marine, il existe des conditions différentes et plus sévères dans le puits.La procédure de qualification des produits chimiques pour l'injection continue de produits chimiques en fond de trou doit prendre en compte ces changements de conditions.La qualification des produits chimiques doit être faite en fonction du matériau avec lequel les produits chimiques pourraient entrer en contact.Les exigences de qualification et de test de compatibilité dans des conditions qui reproduisent aussi fidèlement que possible les diverses conditions du cycle de vie du puits dans lesquelles ces systèmes fonctionneront doivent être mises à jour et mises en œuvre.Le développement de la méthode de test doit être développé davantage pour des tests plus réalistes et représentatifs.
En outre,l'interaction entre les produits chimiques et l'équipement est essentielle au succès.Le développement des vannes chimiques d'injection doit tenir compte des propriétés chimiques et de l'emplacement de la vanne d'injection dans le puits.Il convient d'envisager d'inclure de vraies vannes d'injection dans l'équipement d'essai et d'effectuer des tests de performance de l'inhibiteur de tartre et de la conception de la vanne dans le cadre du programme de qualification.Pour qualifier les inhibiteurs de tartre,l'accent a été mis auparavant sur les défis du processus et l'inhibition du tartre,mais une bonne inhibition du tartre dépend d'une injection stable et continue.Sans injection stable et continue, le potentiel d'échelle augmentera.Si la vanne d'injection d'inhibiteur de tartre est encrassée et qu'il n'y a pas d'injection d'inhibiteur de tartre dans le flux de fluide,le puits et les vannes de sécurité ne sont pas protégés contre le tartre et, par conséquent, la sécurité de la production pourrait être compromise.La procédure de qualification doit prendre en compte les défis liés à l'injection de l'anti-tartre en plus des défis du processus et de l'efficacité de l'anti-tartre qualifié.
La nouvelle approche implique plusieurs disciplines et la coopération entre les disciplines et les responsabilités respectives doivent être clarifiées.Dans cette application, le système de traitement en surface,les gabarits sous-marins et la conception et la complétion des puits sont impliqués.Les réseaux multidisciplinaires axés sur le développement de solutions robustes pour les systèmes d'injection de produits chimiques sont importants et peuvent être la voie du succès.La communication entre les différentes disciplines est essentielle;une communication particulièrement étroite entre les chimistes qui contrôlent les produits chimiques appliqués et les ingénieurs de puits qui contrôlent l'équipement utilisé dans le puits est importante.Comprendre les défis des différentes disciplines et apprendre les uns des autres est essentiel pour comprendre la complexité de l'ensemble du processus.
Conclusion
● L'injection continue d'inhibiteur de tartre pour protéger le DHS Vor le tube de production est une méthode élégante pour protéger le puits contre le tartre
● Pour résoudre les défis identifiés,les recommandations suivantes sont:
● Une procédure de qualification DHCI dédiée doit être effectuée.
● Méthode de qualification des vannes d'injection chimique
● Méthodes de test et de qualification pour la fonctionnalité chimique
● Développement de méthodes
● Tests de matériaux pertinents
● L'interaction multidisciplinaire où la communication entre les différentes disciplines impliquées est cruciale pour le succès.
Remerciements
L'auteur tient à remercier Statoil AS A pour l'autorisation de publier ce travail et Baker Hughes et Schlumberger pour avoir autorisé l'utilisation de l'image de la Fig.2.
Nomenclature
(Ba/Sr)SO4=sulfate de baryum/strontium
CaCO3=carbonate de calcium
DHCI = injection chimique en fond de trou
DHSV = soupape de sécurité de fond
ex=par exemple
GOR=rapport gasoil
HSE = hygiène sécurité environnement
HPHT = haute pression haute température
ID=diamètre intérieur
c'est-à-dire = c'est
km=kilomètres
mm=millimètre
MEG = mono éthylène glycol
mMD=mètre de profondeur mesurée
OD = diamètre extérieur
SI = inhibiteur de tartre
mTV D=mètre de profondeur verticale totale
Tube en U = tube en forme de U
VPD = dépresseur de pression de vapeur
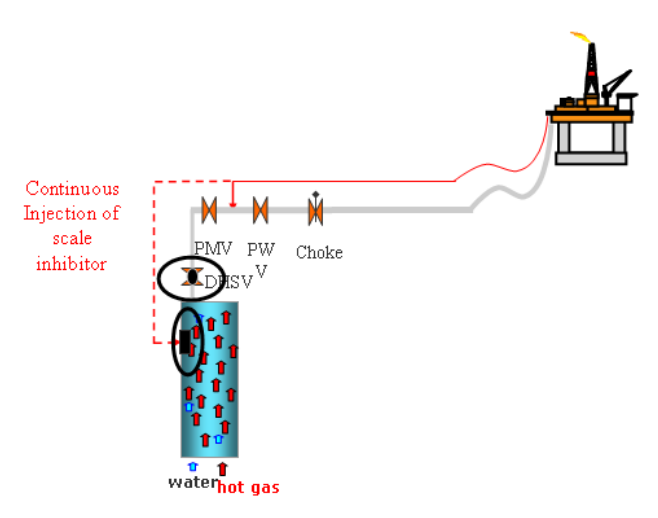
Figure 1. Vue d'ensemble des systèmes d'injection de produits chimiques sous-marins et en fond de trou dans un champ atypique.Croquis de l'injection chimique en amont du DHSV et des défis attendus associés.DHS V = soupape de sécurité de fond de trou, PWV = vanne d'aile de processus et PM V = vanne principale de processus.
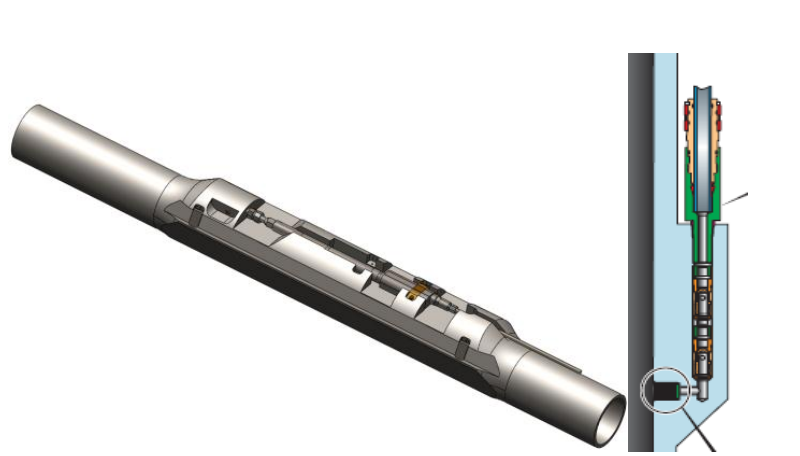
Figure 2. Croquis d'un système d'injection chimique de fond de trou atypique avec le mandrin et la vanne.Le système est relié au collecteur de surface, alimenté et connecté au support de tube sur le côté annulaire du tube.Le mandrin d'injection chimique est traditionnellement placé profondément dans le puits avec l'intention de fournir une protection chimique.
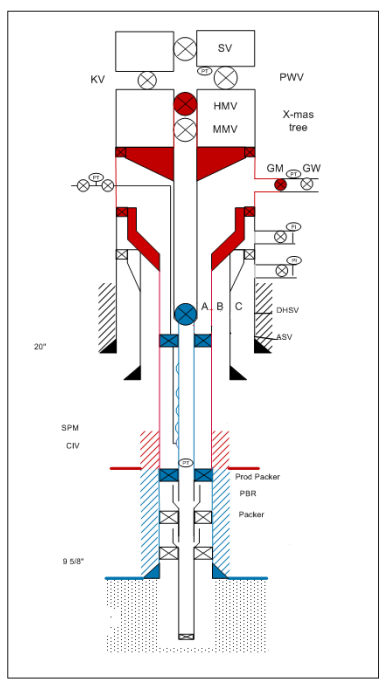
Figure 3. Schéma typique d'une barrière de puits,où la couleur bleue représente l'enveloppe primaire de la barrière du puits ;dans ce cas, le tube de production.La couleur rouge représente l'enveloppe barrière secondaire ;le boîtier.Sur le côté gauche est indiquée l'injection chimique, ligne noire avec point d'injection vers le tube de production dans la zone marquée en rouge (barrière secondaire).
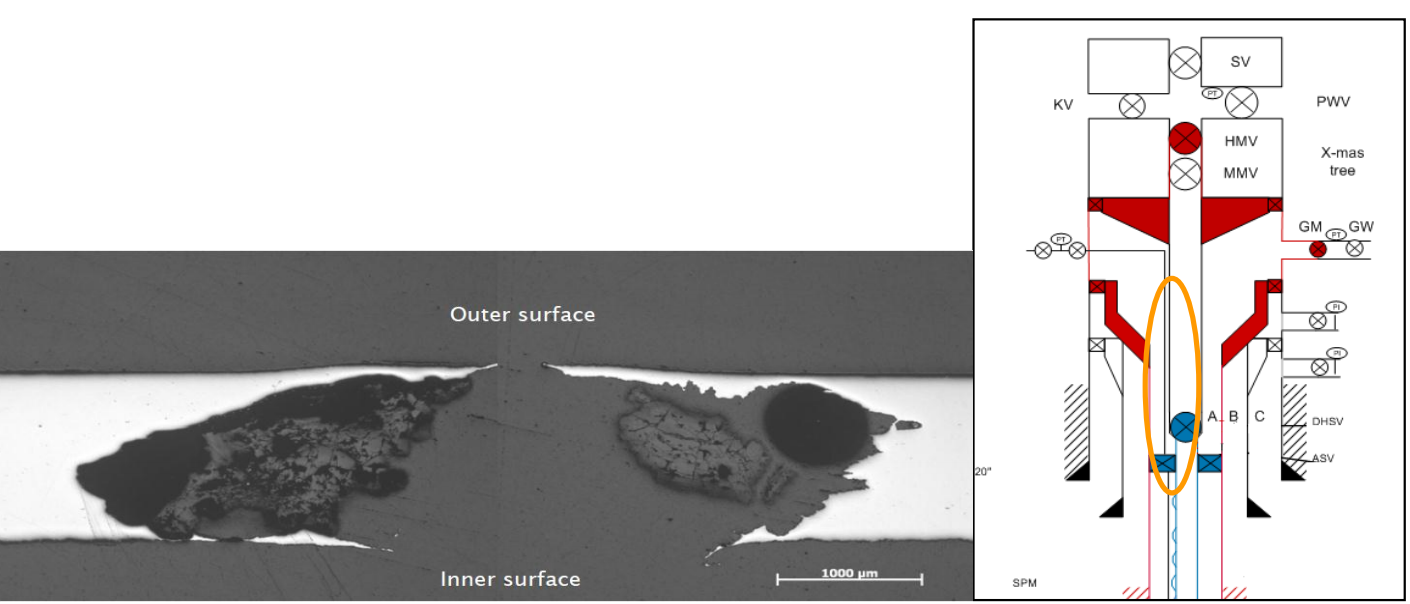
Figure 4. Trou piqué trouvé dans la partie supérieure de la ligne d'injection 3/8".La zone est indiquée dans le croquis du schéma de barrière de puits atypique, marqué d'une ellipse orange.
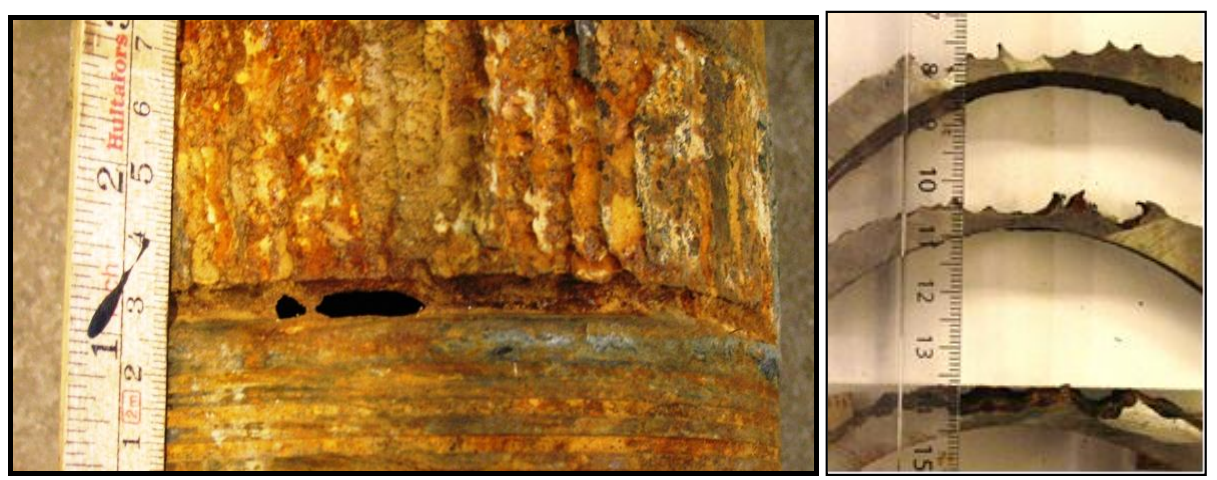
Figure 5. Attaque de corrosion sévère sur le tube 7” 3% Chrome.La figure montre l'attaque de corrosion après la pulvérisation d'un inhibiteur de tartre à partir de la ligne d'injection chimique piquée sur le tube de production.
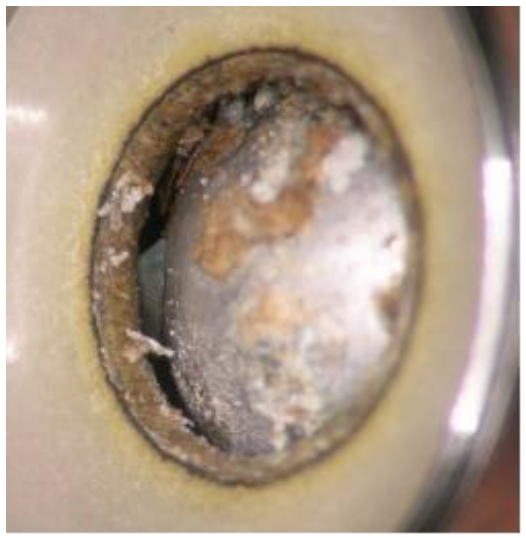
Figure 6. Débris trouvés dans la vanne d'injection de produits chimiques.Les débris dans ce cas étaient des copeaux de métal provenant probablement du processus d'installation en plus de quelques débris blanchâtres.L'examen des débris blancs s'est avéré être des polymères avec une chimie similaire à celle du produit chimique injecté
Heure de publication : 27 avril 2022